Comprehending What is Porosity in Welding: Reasons and Solutions
Comprehending What is Porosity in Welding: Reasons and Solutions
Blog Article
The Science Behind Porosity: A Comprehensive Guide for Welders and Fabricators
Understanding the detailed devices behind porosity in welding is crucial for welders and producers making every effort for impeccable craftsmanship. From the composition of the base materials to the intricacies of the welding process itself, a plethora of variables conspire to either exacerbate or reduce the visibility of porosity.
Understanding Porosity in Welding
FIRST SENTENCE:
Assessment of porosity in welding exposes crucial understandings right into the stability and top quality of the weld joint. Porosity, identified by the visibility of tooth cavities or voids within the weld steel, is a common issue in welding procedures. These gaps, if not properly attended to, can compromise the architectural stability and mechanical residential or commercial properties of the weld, causing possible failings in the completed product.
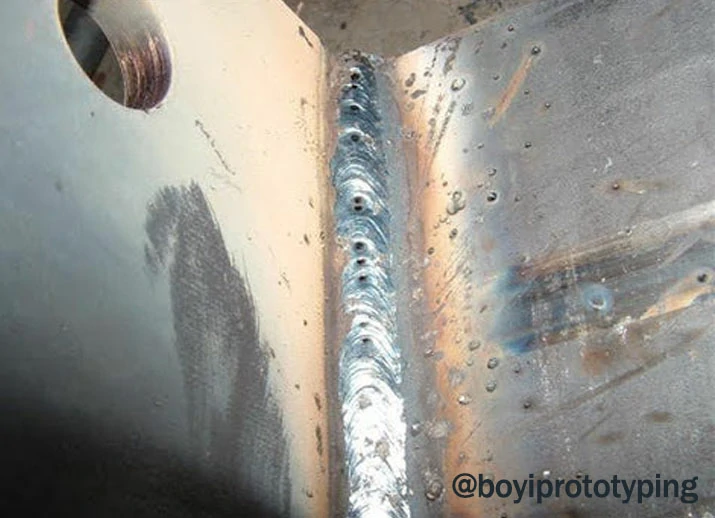
To find and quantify porosity, non-destructive screening approaches such as ultrasonic screening or X-ray inspection are usually used. These techniques enable the recognition of inner issues without compromising the integrity of the weld. By examining the size, form, and distribution of porosity within a weld, welders can make informed choices to boost their welding procedures and accomplish sounder weld joints.

Variables Affecting Porosity Development
The incident of porosity in welding is affected by a myriad of variables, ranging from gas securing performance to the ins and outs of welding specification setups. Welding criteria, including voltage, existing, take a trip rate, and electrode kind, additionally influence porosity development. The welding method used, such as gas metal arc welding (GMAW) or shielded steel arc welding (SMAW), can influence porosity development due to variations in warmth circulation and gas insurance coverage - What is Porosity.
Results of Porosity on Weld Top Quality
The presence of porosity likewise weakens the weld's resistance to deterioration, as the trapped air visit here or gases within the voids can respond with the surrounding setting, leading to degradation over time. Furthermore, porosity can prevent the weld's capability to withstand pressure or effect, more threatening the general quality and dependability of the bonded framework. In vital applications such as aerospace, vehicle, or structural building and constructions, where safety and security and toughness are paramount, the destructive impacts of porosity on weld quality can have extreme consequences, stressing the importance of decreasing porosity through correct welding techniques and treatments.
Techniques to Lessen Porosity
In addition, utilizing the ideal welding specifications, such as the right voltage, current, and travel rate, is important in avoiding porosity. Preserving a consistent arc size and angle throughout welding additionally aids lower the possibility of porosity.

In addition, picking the appropriate protecting gas and keeping correct gas circulation prices are crucial in minimizing porosity. Using the ideal welding technique, such you could try here as back-stepping or using a weaving motion, can also aid distribute warm evenly and reduce the Bonuses chances of porosity formation. Ensuring correct air flow in the welding setting to get rid of any prospective resources of contamination is important for achieving porosity-free welds. By applying these strategies, welders can effectively minimize porosity and generate top notch bonded joints.
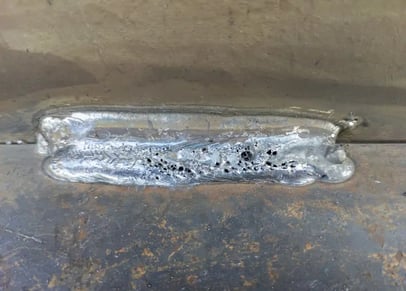
Advanced Solutions for Porosity Control
Executing innovative innovations and ingenious methods plays an essential role in attaining exceptional control over porosity in welding processes. One innovative remedy is using advanced gas blends. Protecting gases like helium or a blend of argon and hydrogen can help in reducing porosity by providing much better arc stability and boosted gas insurance coverage. In addition, employing advanced welding techniques such as pulsed MIG welding or modified ambience welding can also aid minimize porosity concerns.
One more advanced remedy entails using sophisticated welding tools. Using tools with built-in features like waveform control and sophisticated power resources can boost weld top quality and minimize porosity risks. The application of automated welding systems with specific control over specifications can significantly minimize porosity flaws.
Additionally, including advanced tracking and examination innovations such as real-time X-ray imaging or automated ultrasonic screening can assist in identifying porosity early in the welding process, enabling immediate corrective activities. Generally, incorporating these sophisticated remedies can greatly boost porosity control and improve the total high quality of bonded elements.
Verdict
To conclude, recognizing the scientific research behind porosity in welding is crucial for welders and fabricators to produce premium welds. By identifying the elements influencing porosity development and applying methods to decrease it, welders can improve the general weld high quality. Advanced remedies for porosity control can further improve the welding procedure and guarantee a solid and reputable weld. It is necessary for welders to constantly inform themselves on porosity and execute best practices to achieve ideal outcomes.
Report this page